Waterproofing
GreenGrid has been designed to be compatible with most commercially available low-slope waterproofing systems. This includes many common applications using single-ply membranes such as TPO, EPDM, and PVC as well as other high-quality applications such as hot or cold fluid applied systems and built-up roofing (BUR). While GreenGrid is compatible with numerous systems, some surface preparation materials and procedures will vary by manufacturer. Please contact your selected waterproofing manufacturer for specific preparations necessary for installation of your GreenGrid green roof.
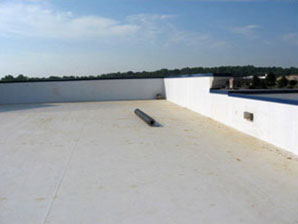
Watertightness First!
To a building owner, the beauty of a lavish vegetative green roof is quickly obscured when the roofing system below it starts to leak. To ensure a watertight installation under a green roof, the following steps should be taken by the building owner, architect, and roof contractor:
Over Design the Roofing System
In a vegetative green roof application, the roofing membrane is buried beneath the vegetation and the more the waterproofing system can be enhanced to extend longevity, the better the overall application will be.
Go with a thicker membrane for better puncture resistance. With single-ply membranes, 60 mil should be considered the minimum thickness to use in a green roof application.
On more elaborate vegetative green roof designs or if extended roofing warranties are desired, consider using the thickest membranes available in that product line.
Strip in the seams. To ensure a strong seam, specify a minimum 6-inch stripping over all seams to provide redundancy.
To prevent possible abrasions or punctures, try to eliminate any mechanical fasteners directly below the membrane. If attaching insulation, use adhesives for the top layer.
Flashings in a vegetative green roofing system are vulnerable to damage because they are subjected to the differential movement that exists between the roof deck and vertical surfaces.
Flashings should extend a minimum of 8 inches above the surface of the membrane and at least 4 inches above the surface of the growing medium.
Installing metal counter flashings over the membrane flashings will provide additional protection from physical damage throughout the service life of the vegetative roofing system.
Sealing the top edge of the membrane flashings with sealant and termination bar is critical to maintaining a watertight seal at the flashings.
Fully Inspect/Water Test the Roofing System
It is imperative that the waterproofing system be tested for leaks prior to the installation of the vegetative roof. It makes the most sense to test the integrity of the membrane for watertightness while it is still fully exposed for easy access. There are three basic methods to test a roofing system for leaks prior to installing the vegetative components:
Flood Test
A standing water test. The roof drains are plugged and dams are built to retain water on top of the waterproofing membrane. Water depth should be a minimum of 2 inches and left on the roof surface for at least 24 hours.
Advantages: Exerts hydrostatic pressure over the entire surface of the membrane, which is the ultimate test of a waterproofing membrane.
Disadvantages: Time consuming because only small areas should be tested to prevent overloading the structure. In addition, slope in the roof may mean much deeper depths downslope to create the required 2 inches on the upslope end.
Flowing Water Test
Continual flow of water over the roof surface for a minimum of 24 hours, without blocking the drains or construction dams.
Advantages: Excellent alternative to flood testing on sloped roofs or on roofs that do not have the structural capacity to support 2 inches of ponding water.
Disadvantages: Only tests the roof surface and does not test the flashings. Does not put the roofing membrane under hydrostatic pressure, which may miss some of the smaller, difficult-to-find voids or punctures.
Electronic Field Vector Mapping
Uses DC current and water (with a surfactant) to test for breaches in the roofing membrane. An electric potential is created by placing a conductor below the roof membrane (generally the roof deck and framing) and energizing the roof surface by the use of a grounded loop placed on the surface. Water spread over the surface of the roof will pass through a puncture and complete a circuit. Since DC is single directional, the puncture can be located by following the flow of current.
Advantages: Very precise. Conductors can be left in place and reused throughout the life of the system, which makes pinpointing leaks in the installed system much easier and eliminates the need to remove large areas of vegetation and overburden.
Disadvantages: Expensive compared to flood and running water testing. Will not work on EPDM and may not work with aluminum-coated membranes, due to conductivity of membranes. Nonconductive roof decks require additional conductor installation before new waterproofing membrane is installed.
Protect the Membrane
All vegetative green roofing systems should have some type of membrane protection, such as protection boards or fabric mats. Also, membrane protection must be increased in areas of heavy traffic and under designated walkways. It is very important that the roofing membrane be protected during the installation process. Plywood and other hard-surface protection boards must be used at access points and travel paths during installation.
Ask the waterproofing manufacturer if a root barrier is required or what thickness of protective mat is needed.
Maintain the Roofing System After Installation
As with any roofing system, regular maintenance is important. Don’t be misled by thinking that because the membrane is buried under a vegetative green roof, there is nothing you can do to maintain the roof. Here are regular maintenance items that should be done on a green roof:
- Clean drains twice a year
- Inspect flashings for deterioration
- Check sealant at terminations for deterioration
- Inspect after major storms
Understanding Roofing and Waterproofing Principles
Low-slope roofing differs from common steep slope (residential) roofing because low-slope roofing systems must be WATERTIGHT where steep-slope roofing systems need only be WATER SHEDDING. Because low-slope roofing systems must be watertight, the slightest hole or puncture will admit water into the systems, creating a leak.
Insulation
Consideration should be given to the types of insulation used in a vegetative green roof application.
Avoid the use of porous insulations and focus on closed-cell-type insulations to avoid trapping moisture within the roofing system.
Recommended Closed-Cell Insulations:
- Extruded Polystyrene
- Polyisocyanurate
- Gypsum based Dens Deck
In addition to limiting the porosity of the roof insulation, ensure that higher compressive strength insulation is specified to prevent compression by the overburden.
Drainage
Like any roofing system, positive drainage is very important. Minimum slope should be 1/4 inch per foot. Structural slope is preferred over tapered insulation. The drainage layer not only provides a means for stormwater to exit the roof, it also can provide air movement under the growing media to help dry the insulation. Vegetative green roofing systems should always be internally drained. Edge draining should be avoided to prevent loss of components and growing medium at the building perimeter during high wind or precipitation events.
Retrofit Project Considerations
Built-in-place vegetative green roof systems do not lend themselves to retrofit applications. Modular applications are more “user friendly” when designing a retrofit.
Integrity of existing roof system:
- What has been the service life of the roof? – If the service life of the roof is reaching its end and starting to have small issues such as minor leaks and deterioration, the roof system is probably not conducive to a vegetative roof.
- Is the roof system capable of accepting a vegetative green roof system? – It is important to confirm with the manufacturer the acceptability of a vegetative roof system over an existing roof system. Installing a vegetative roof system on an existing roof system could void the balance of the manufacturer’s warranty.
- Is the roof watertight? – Just as with a new application, the existing roof system needs to be completely watertight and in good repair. You do not want to have to go in and make roof repairs after the vegetation is installed. Is the structure capable of handling the additional loads required?
- Is the structure capable of handling the additional loads required?
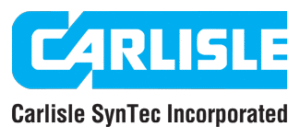
GreenGrid has been partnering with Carlisle Syntec, Inc. (Carlisle) since 2006 and collaborated on numerous high profile GreenGrid installations across the U.S.
Carlisle’s products are uniquely suited to GreenGrid and Carlisle’s GreenGrid Roof Garden system provides a variety of waterproofing options with a full line of accessories to insure a high performance system. This includes a range of membranes such as the 60-mil EPDM and TPO which are ideal for the Extensive Roof Gardens with standard 15 to 20 year warranties. GreenGrid Roof Gardens most often require 75-mil EPDM or 72-mil TPO membranes for 10-15 year warranties, and 90-mil EPDM or 80-mil TPO membranes for 20 year warranties. For the Intensive Carlisle GreenGrid Roof Gardens the membrane options include Carlisle’s toughest membranes, the 90-mil EPDM, 80-mil TPO and the 115 through 145-mil FleeceBACK¨ membranes. These are examples of the myriad options offered to you through this program with varying levels of warranty up to the full-system warranty which covers waterproofing and green roof overburden removal and replacement.
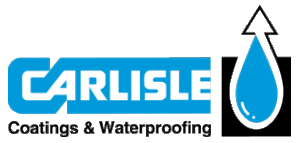
Carlisle Coatings & Waterproofing, Inc. (CCW) is a results focused organization that provides a very broad range of solutions to meet your waterproofing needs. CCW offers a complete line of waterproofing and moisture protection products for the construction and architectural communities. The CCW GreenGrid system is based on their 500GR Reinforced Hot Applied Liquid Membrane System. The combination of a CCW waterproofing system and GreenGrid creates a completed warranted roof assembly that meets each individual customers needs.